31.05.2021. In the ReHyb project, TECNALIA focuses on the development and integration of multichannel Functional Electrical Stimulation (FES) and Electromyography (EMG) technologies into the ReHyb exoskeleton systems. We are developing a new, distributed wrist and hand neuroprosthesis that synergistically works together with a wearable exoskeleton. TECNALIA provides both the Hardware and Firmware and the body-worn electrodes for integrating into exoskeletons and a joint multilevel control architecture. In this integration task, researchers at TECNALIA, SSSA and IUVO are working closely together on modular integration and usability aspects. The integration of a garment with the exoskeleton will be at a morphological, but also at a functional level, thus allowing the optimal fitting to personalized robotic devices.
When defining the electrodes for an exoskeleton, the analysis of effects of the garment integration with exoskeleton fixtures and the impact of movements on the EMG signal quality are important aspects. With this objective, a series of tests have been performed to check if the pressure and/or movement on the EMG electrodes have any negative effect or artifacts on the recorded signals.
A mock-up of a module of the exoskeleton that will be developed within the ReHyb framework has been assembled by IUVO to enable qualitative tests on the possible impact of the cuff-arm pressure on the FES system functionality. It basically consists of a lockable elbow joint attached to the arm and forearm by means of two cuffs.
For the first analysis, wrist flexion/extension and pronation/supination have been selected since the involved muscles are totally or partially covered by the exoskeleton mock-up (Figure 2). During preliminary tests, both commercial electrodes and custom-made array electrodes were placed on wrist extensors, wrist flexors and the pronator teres using bipolar mode recording. A protective garment was attached over the electrodes (Figure 1 right), that in addition to making pressure on them will ensure the correct position. A sequence of the selected movements has been executed in this configuration.
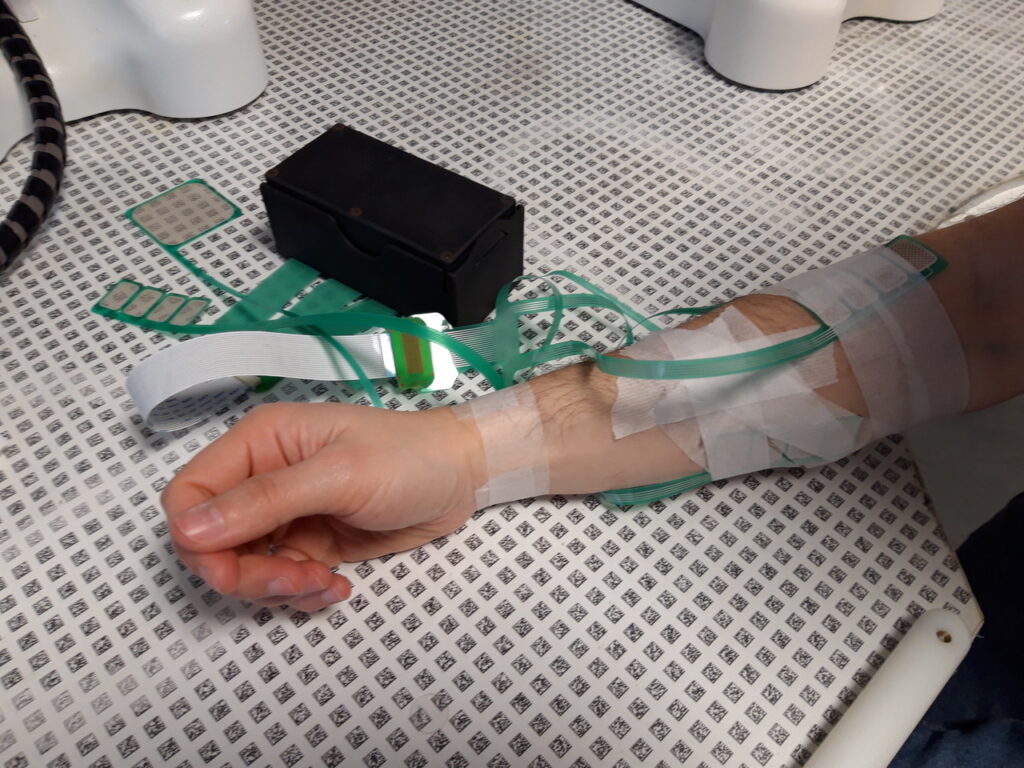
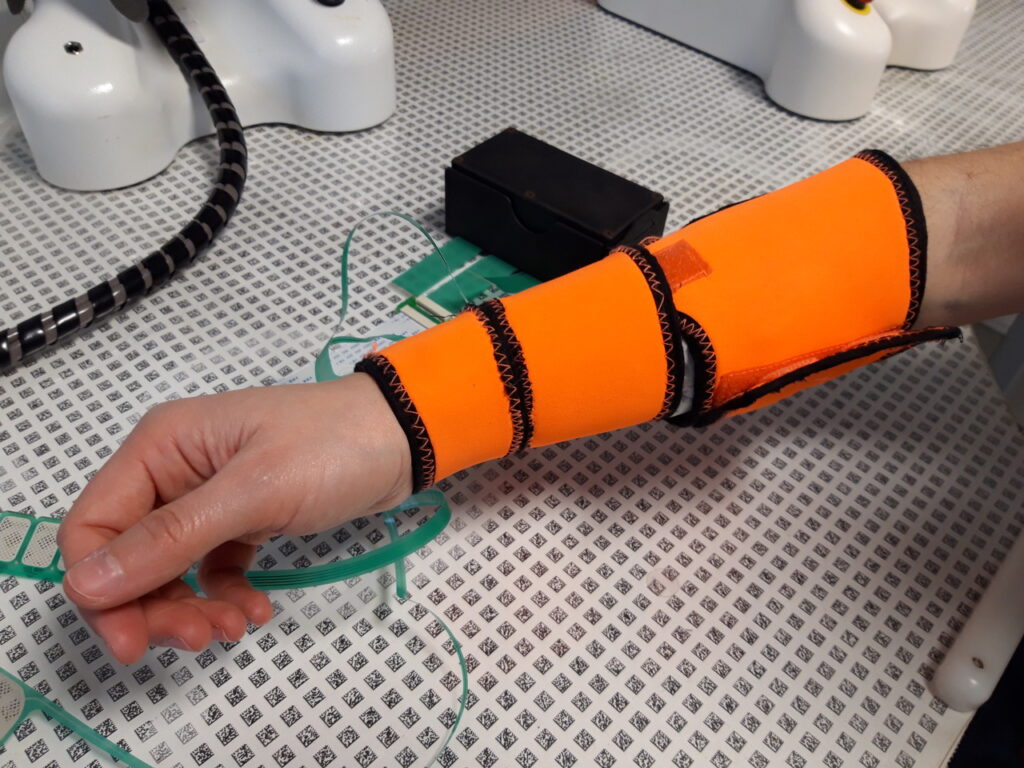
Figure 1: [left] custom-made array electrodes with no garment (baseline); [right] electrodes covered by the garment
Then, the mock-up of the passive lockable elbow exoskeleton developed by IUVO (Figure 2) has been added and the same sequence was repeated.
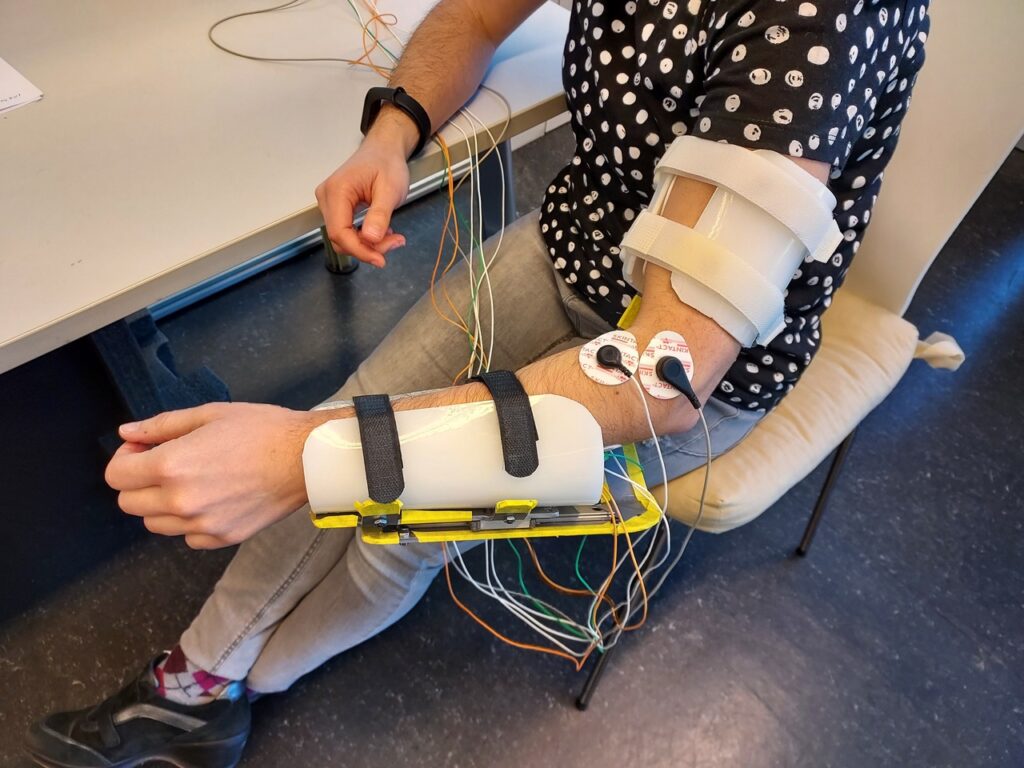
Figure 2: Elbow exoskeleton mock-up
From a preliminary analysis, it has been highlighted that introduced motion and pressure artifacts can be removed with signal processing and muscle activity is well detected.